Getting More from Your Electroless Nickle Tank
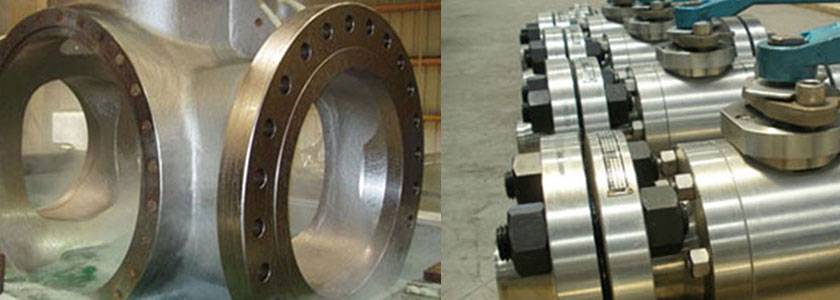
For owners and managers of metal plating companies, the enduring performance of high quality electroless nickel chemistry is a fundamental priority. A combination of meticulous process control, appropriate tank equipment, and the right choices of filter media for plating tanks can significantly extend the operational lifespan of your electroless nickel baths.
Electroless nickel plating is a process that relies heavily on the balance and purity of its chemical bath. To maintain this crucial equilibrium, the role of suitable filter tubes cannot be overstated. The right filter cartridges are the frontline defense against particulate contamination, directly affecting bath lifespan and the quality of plating outcomes.
Selecting the right filtration equipment requires careful consideration of the specific demands of your electroless nickel process. One must consider the filtration rate, dirt holding capacity, chemical resistance, and temperature resilience. Media like activated carbon and polypropylene are popular choices, as they are resistant to caustic chemicals and can efficiently capture organic and inorganic impurities. Filter media like these ensure that your bath maintains optimal cleanliness and efficiency, directly contributing to the quality of your electroless nickel deposits.
However, achieving a high-quality finish and long bath life isn’t solely about maintaining a clean bath. Controlling the bath’s temperature is equally pivotal, warranting the proper selection and use of electroplating tank heaters. In electroless nickel processes, temperature influences deposition rates, phosphorus adhesion, and the resultant deposit’s characteristics.
The type of heater used in your electroplating tanks can directly affect your ability to control these factors. Over-the-side heaters and immersion heaters are common types utilized within the industry. Over-the-side heaters are an excellent choice for tanks with limited space, as they are designed for easy installation and removal. On the other hand, immersion heaters, which directly heat the solution, offer rapid heat-up times and precise temperature control, essential factors in managing an electroless nickel bath’s behavior.
Material compatibility of heaters with plating solutions is a critical consideration. Heaters with titanium components like the Process Technology heaters are often preferred due to their high resistance to most chemicals. In contrast, for baths with acidic characteristics, quartz heaters provide an optimal solution due to their high resistance to corrosion.
In sum, maximizing the lifespan of electroless nickel chemistry is a multifaceted challenge. It requires a carefully chosen filtration equipment that uses the appropriate filter media, as well as a compatible and effective electroplating tank heater. By making informed decisions regarding these critical components, you can ensure a stable, high-quality electroless nickel process that produces consistent, high-quality finishes and a prolonged bath lifespan.
Keeping abreast of the latest advances in filtration media and heaters is part of the job. As technology continues to advance, newer and more efficient options will become available, providing even greater opportunities for optimizing your electroless nickel processes. Make no mistake, making the right choices here is a long-term investment in the quality of your operations and the satisfaction of your customers. It’s worth taking the time to ensure you’re making the best decisions for your business.